Ahena Boilers
Biomass Boilers – Moving Grate
Biomass Boilers – Moving Grate
Serie MRG
The hot water generators of the MRG series are designed with a structure in two overlapping parts; the combustion system is located in the lower part while the horizontal smoke tube heat exchanger is in the upper part. The entire generator is made with water-jacketed walls, a solution that optimizes thermal exchange and prolongs the life of refractory materials.
To further increase efficiency, the heat exchanger can be designed with three smoke passes.
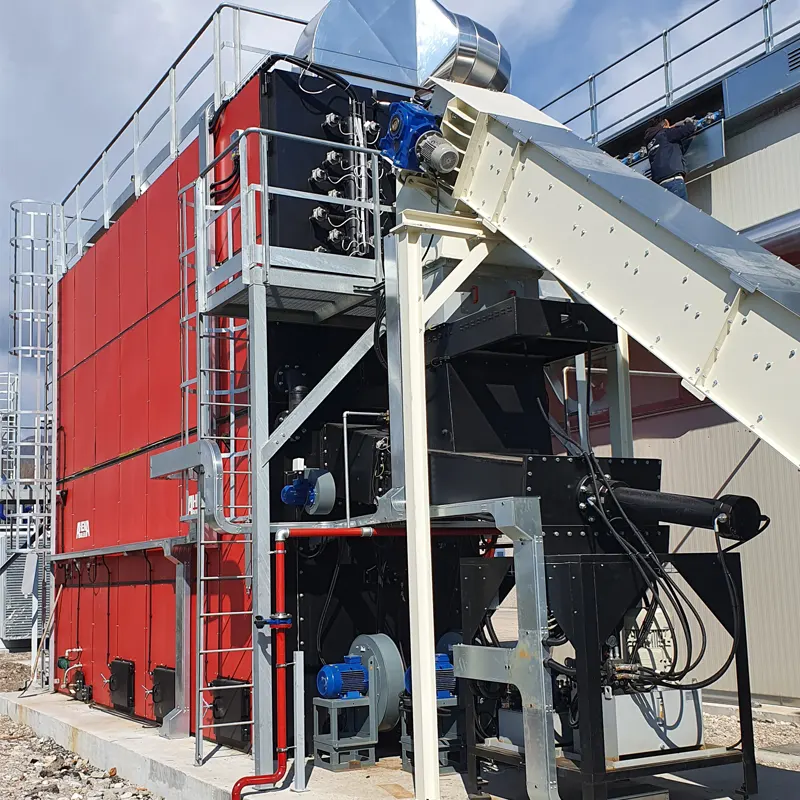
Technical Specifications
- Two-Section Structure:
- Base Foundation: houses the combustion system and ensures robustness and resistance over time.
- Heat exchanger: with horizontal smoke tubes, designed to improve thermal efficiency.
- Water-Jacketed Walls: Innovative solution that optimizes thermal exchange and prolongs the life of refractory materials.
- Heat Exchanger with Three Smoke Passes: Advanced configuration option to increase energy efficiency.
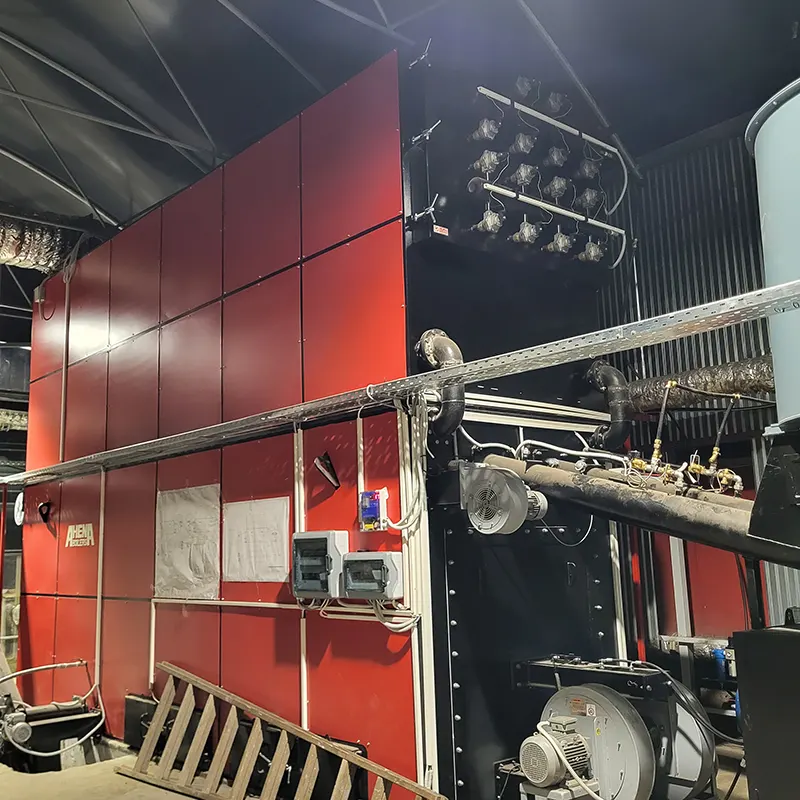

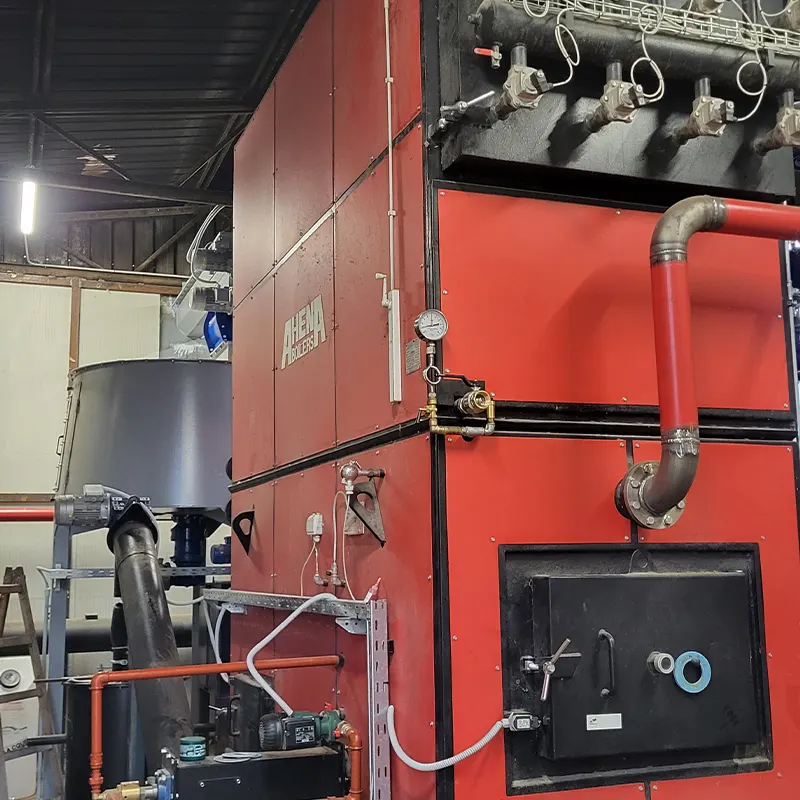
Advanced Combustion System
- Moving Step Grate: Made with high-chromium steel elements to withstand high temperatures and ensure efficient combustion.
- Customized Dimensions: The grate surface is adapted based on the required power and the type of fuel used.
- Air Distribution:
- Primary air: under the grate, divided into distinct zones with dedicated fans.
- Secondary and tertiary air: injected through lateral nozzles above the grate to optimize combustion.
- Fuel Supply:
- Through screw conveyor for particles up to 50 mm.
- Through pusher for larger-sized fuels.
- Supports fuels with moisture content up to 50%.
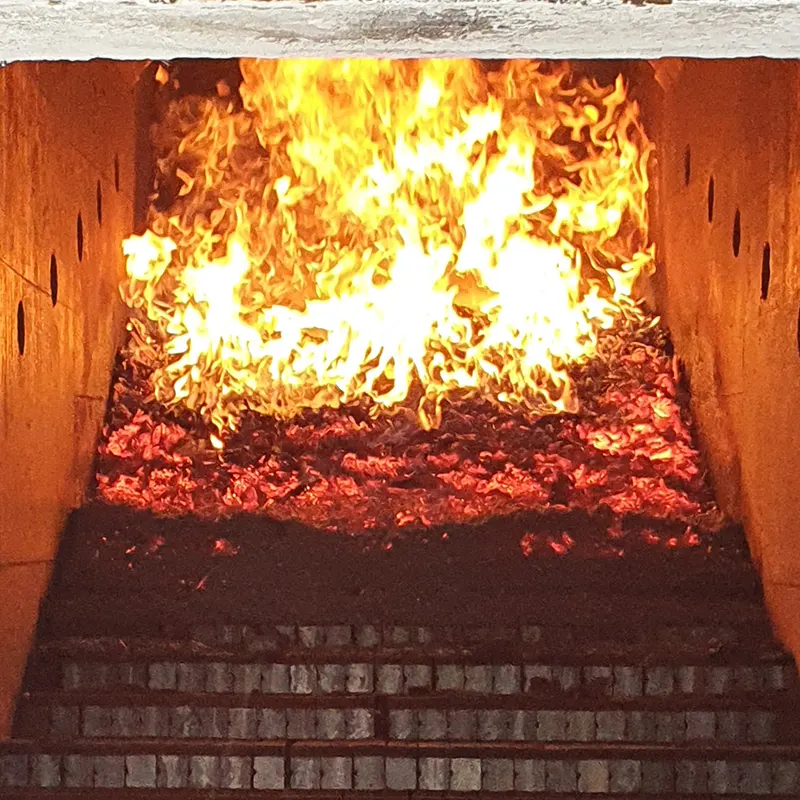
Moving Grate Combustion System
The technological heart of the MRG generators is the moving step grate combustion system, characterized by:
-
- Step elements in high-chromium alloy steel (>30% Cr) with metallurgical properties optimized to withstand extreme thermo-mechanical stress
- Variable speed hydraulic drive, with electronic control of movement to optimize fuel advancement based on its characteristics
- Grate surface sizing, according to the following critical parameters:
- Required nominal thermal power
- Lower heating value (LHV) of the fuel
- Bulk density and particle size of the fuel
- Moisture and ash content
- Ash melting temperature
The moving grate technology allows effective management of the combustion phases, ensuring optimal control even with biomass characterized by high heterogeneity and high moisture content.
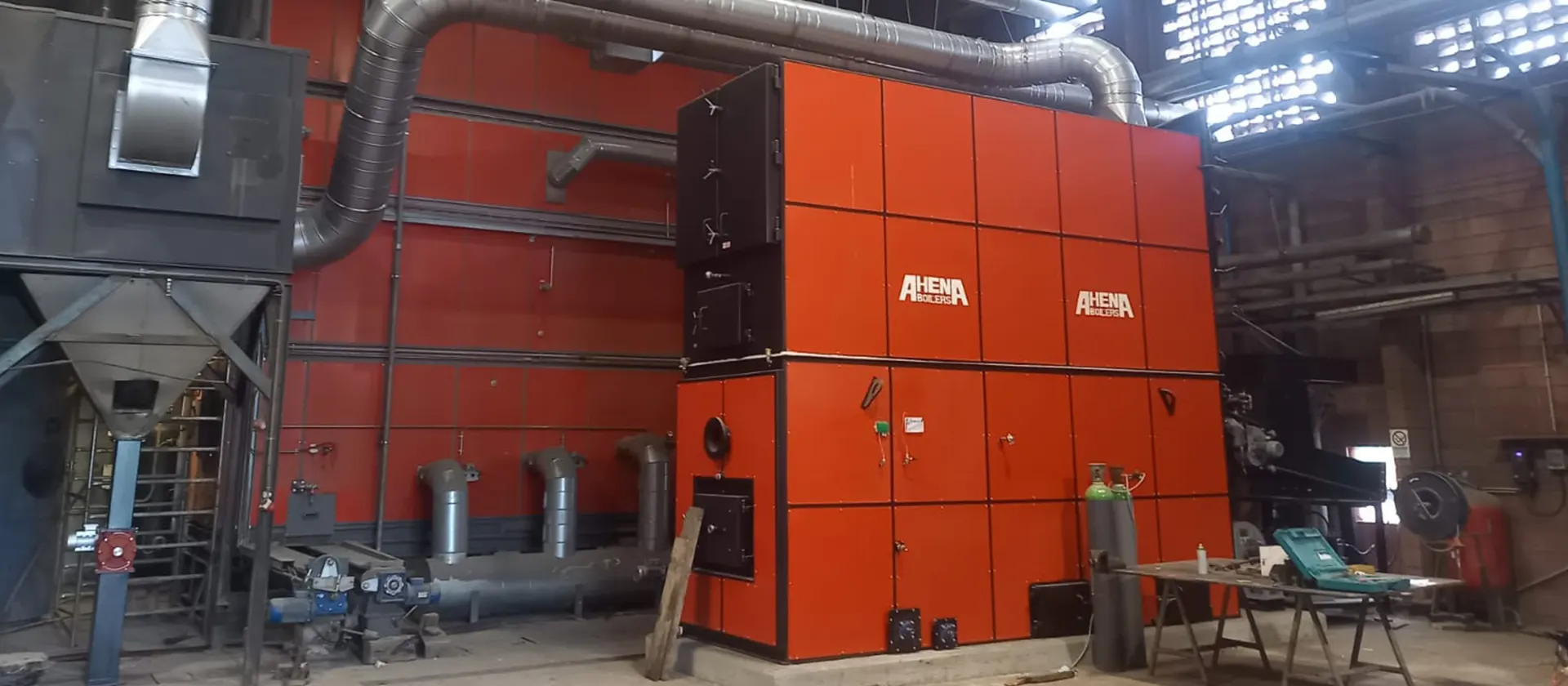
Plant Management
The management of the entire plant is entrusted to a PLC software developed over the years and optimizable for each installation.
The software allows complete control of the plant even remotely, in particular:
- Manages the smoke extractor via inverter to ensure constant negative pressure in the combustion chamber
- Manages all combustion air fans via inverters to optimize combustion in every phase
- Manages the fuel supply via inverter, modulating the quantity introduced into the boiler to achieve a wide range of available power based on thermal consumption
- Detects all main parameters through sensors for full plant control, specifically detecting:
- All temperatures of Water, Smoke, Combustion Chamber
- Feed system temperature as fire safety
- Lambda sensor for oxygen management in the flue gases
- Combustion chamber negative pressure
- Fuel presence sensors
Cleaning and Maintenance
The MRG generators are designed for easy maintenance management, thanks to:
- Wide access doors for easy inspection of the heat exchanger.
- Ash Extraction System:
- Combustion chamber.
- Under-grate zone.
- Pneumatic Tube Bundle Cleaner: Reduces the frequency of routine cleaning interventions.

Power Range and Configurations
- Available Power: from 300 kW up to 6 MW.
- Customizable Foundation:
- Completely lined with refractory materials to ensure resistance and durability.
- Configuration option with or without internal arch to optimize flue gas path in co-current or counter-current.
Optimal Industrial Applications
The MRG series generators find preferential application in industrial and production contexts characterized by:
- High energy requirements with availability of local heterogeneous biomass
- Need for operational flexibility in handling fuels of variable quality
- Requirement for service continuity with reduced maintenance interventions
- Environmental sustainability objectives and energy cost containment
Main application sectors:
- Wood and forestry processing industrial districts
- Medium and high power district heating plants
- Agri-food and process industry
- Production complexes with high thermal energy requirements

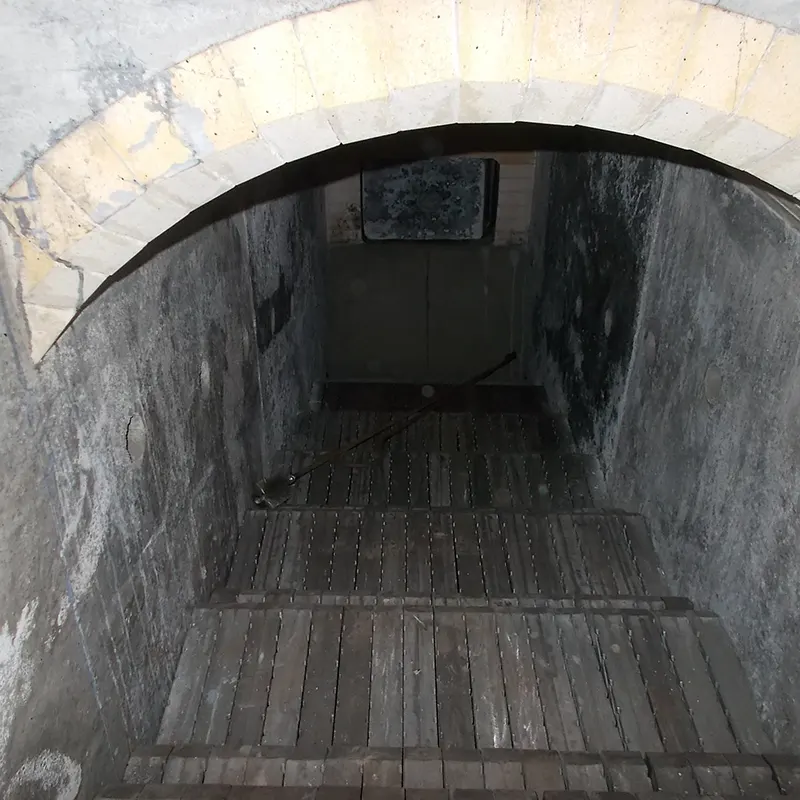
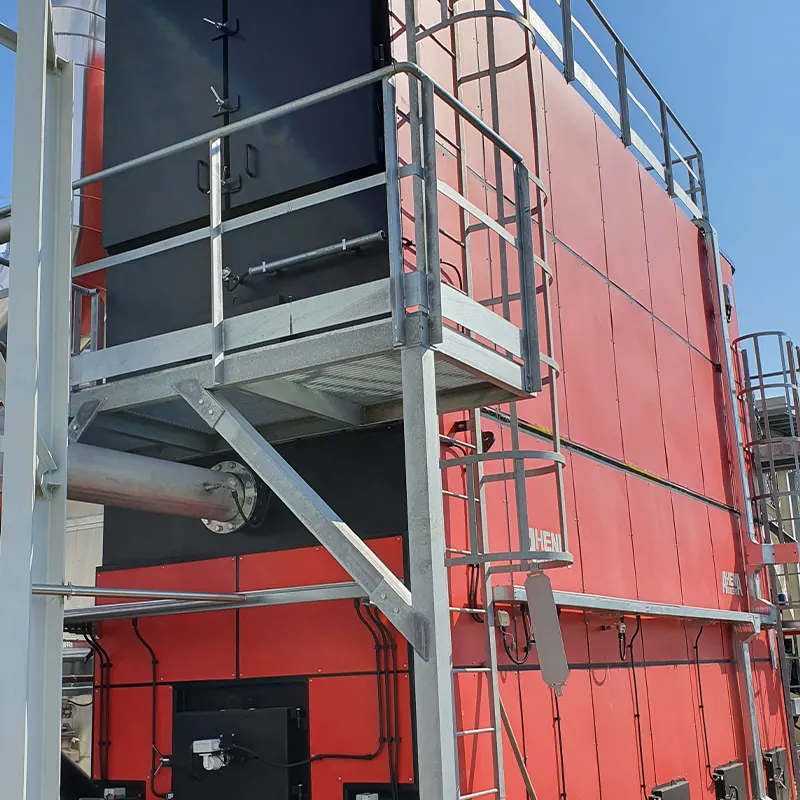