Ahena Boilers
Steam Generators
GV Series Biomass Steam Generators
The GV series steam generators represent an advanced solution for steam production, combining high efficiency, versatility and robustness. Designed with a two-section overlapping structure, they ensure optimal combustion and heat exchange management, ensuring high performance and compliance with the strictest safety regulations.

Two-Section Configuration
The design of GV generators is characterized by a modular architecture with two overlapping sections:
-
- Lower section (foundation): houses the combustion system with dry chamber, fully made with high-density refractory and insulating panels
- Upper section: integrates the cylindrical smoke tube heat exchanger with horizontal layout, designed according to the PED 2014/68/EU Directive to operate under high pressure conditions
The heat exchanger is sized according to specific application requirements, with configuration options for operating pressures up to 18 bar, each exchanger is designed with a large steam space to allow for smaller pressure fluctuations during the use phase.



Configurable combustion systems
The GV series generators offer two different combustion system configurations, selectable based on fuel characteristics and operational requirements:
- Fixed Flat Grate System
- Moving Step Grate System
Both configurations are characterized by a "dry" foundation, with refractories of high thermo-mechanical resistance and thick thermal insulation made of multilayer panels. The combustion chamber geometry can be customized with or without internal arch, to optimize the flue gas path in co-current or counter-current regime, depending on the specific characteristics of the fuel.
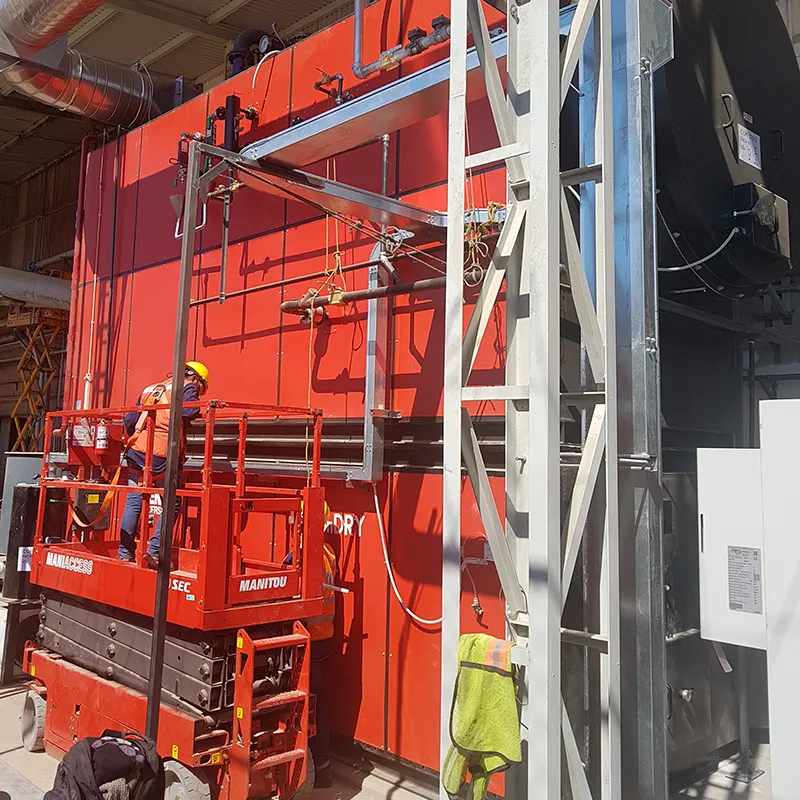
Advanced combustion air management
The combustion air distribution system is designed according to a zone approach:
- Primary air: distributed under the grate in distinct zones, with independent flow regulation to optimize combustion
- Secondary air: injected through nozzles positioned on the side walls of the combustion chamber
- Tertiary air: Used for some fuels to achieve complete combustion and efficiency
- Integrated electronic control: based on residual oxygen sensors (lambda probes) and temperature, ensures constant maintenance of optimal combustion parameters, maximizing efficiency and minimizing emissions
The automatic air/fuel system regulation allows maintaining high efficiency even under partial load conditions, dynamically adapting to qualitative variations in fuel.

Fuel feed systems
The GV generators are configurable with two different feed systems:
- Mechanical screw system:
- Compatible with biomass having particle sizes up to 30-50 mm
- Drive via gearmotor with speed control
- Above-grate feeding for moving grate system
- Underfeed type below grate for fixed grate system
- Hydraulic pusher system:
- Suitable exclusively for moving grate system
- Indicated for heterogeneous fuels with particle size over 50mm
- Actuation via hydraulic cylinder
- Proportional fuel management based on required power
The configuration of the feed system is selected during the design phase, based on the specific characteristics of the biomass available at the customer's plant.

Integrated Solutions for Simplified Maintenance
The design of GV generators incorporates advanced solutions to minimize maintenance interventions and simplify cleaning operations:
- Enlarged inspection doors with simplified opening system, sized to allow ergonomic access to the heat exchanger
- Automated extraction system ash from the combustion chamber, with mechanisms resistant to high temperatures
- Optional sequential pneumatic cleaning system of the tube bundle, with programmable actuators to minimize deposit formation on heat exchange surfaces
- Complementary ash extractor for the area below the grate, for collecting fines that have percolated through the grate elements
The integration of automated ash management and heat exchanger cleaning systems allows for a significant increase in plant operational autonomy, reducing the frequency of manual maintenance interventions and ensuring optimal performance is maintained over time.
Dimensional and Performance Range
The GV series covers a wide spectrum of industrial applications with a complete range of production capacities:
- Steam production range: from 350 kg/h to 8,000 kg/h
- Maximum operating pressure: up to 18 bar
- Steam temperature: saturated steam at temperature corresponding to operating pressure
- Overall thermal efficiency: up to 88%
The generator configuration is customizable based on fuel characteristics and specific operational requirements, with the possibility of integrating economizers, air preheaters and advanced energy recovery systems to maximize the overall plant efficiency.

Regulatory Compliance and Operational Safety
The GV series generators are designed and built in compliance with the most stringent European industry regulations:
- Pressure Equipment Directive 2014/68/EU (PED), with classification in Category IV
- Machinery Directive 2006/42/CE
Each generator is equipped with a complete system of safety devices and protections:
- Safety valves in accordance with ISPESL/INAIL standards
- Safety pressure switches and thermostats
- Category IV self-controlled minimum and maximum level systems
- Level indicators and controllers
- Continuous conductivity control
- Automatic bottom and surface blowdown valves
Design, production and testing are carried out under the supervision of a Notified Body to ensure full compliance with applicable regulatory requirements.
Optimal Industrial Applications
The GV series steam generators find preferential application in industrial and production contexts characterized by:
- Industrial processes requiring medium-high pressure steam
- Need to reduce energy costs compared to fossil fuels
- Availability of waste biomass from production processes
- Environmental sustainability objectives and CO₂ emission reduction
Main application sectors:
- Food and pharmaceutical industry
- Chemical and petrochemical sector
- Textile and paper industry
- Industrial processing with high technological steam requirements
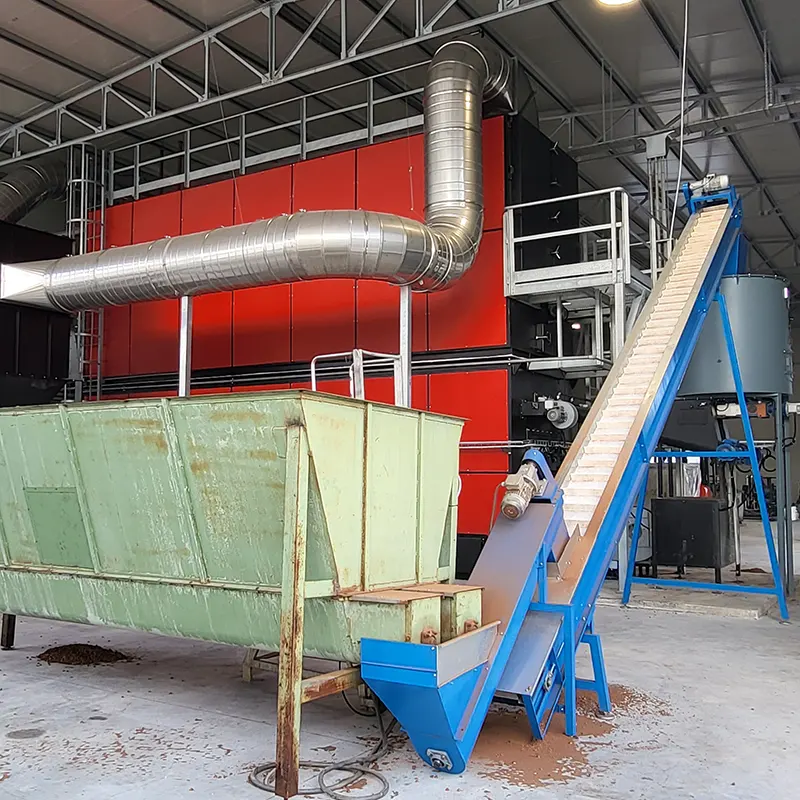

