Ahena Boilers
Biomass Boilers – Fixed Grate
MR series hot water generators
The MR series hot water generators are designed with a monoblock structure, which integrates the combustion system in the lower part and the horizontal smoke tube heat exchanger in the upper part. The entire generator is made with water-jacketed walls, a solution that optimizes thermal exchange and prolongs the life of refractory materials.
To further increase efficiency, the heat exchanger can be designed with three smoke passes.

Technical Specifications
- Monoblock Structure: Compact design for easy installation and maintenance.
- Water-Jacketed Walls: Improves thermal exchange efficiency and prolongs the generator's life.
- Smoke Tube Heat Exchanger: Available with three smoke passes for optimized efficiency.
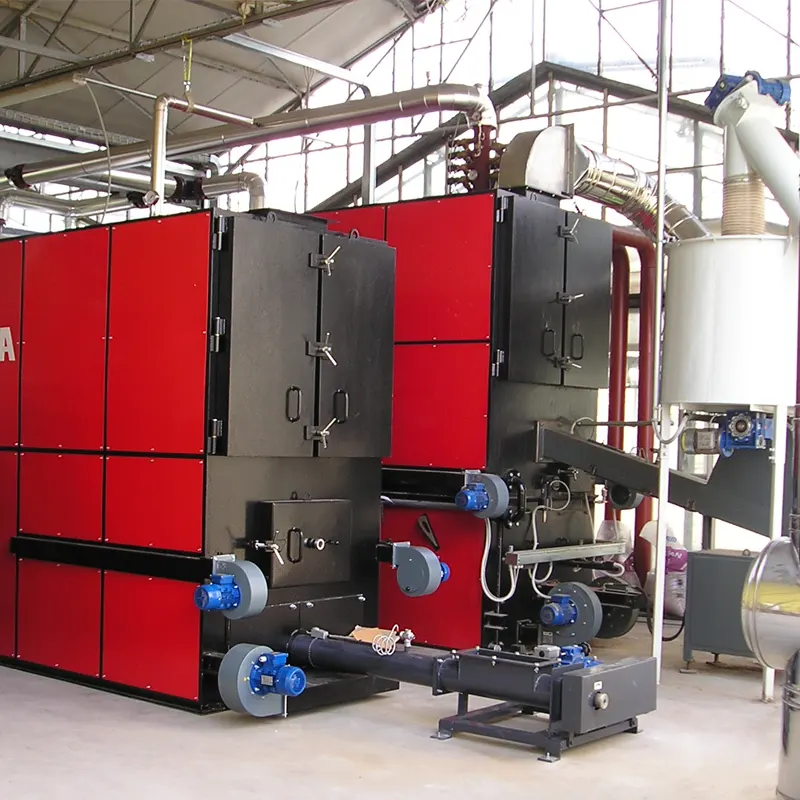
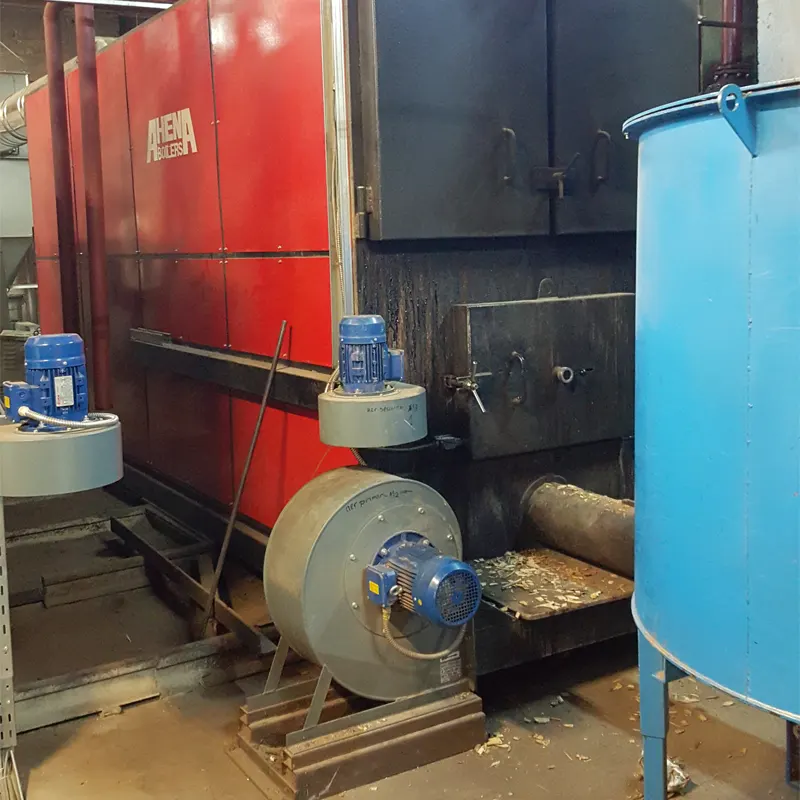

Combustion System
- Fixed Grate: Made with refractory steel elements, thanks to its simplicity and reliability it allows optimal combustion of dry material.
- Refractory-Lined Combustion Chamber: Possibility of installing an internal arch to optimize combustion and flue gas path.
- Feed System: The fuel is fed through a screw conveyor, supporting materials with maximum particle size of 30 mm and moisture up to 35%.
- Combustion Air Management:
- Primary air under the grate distributed in distinct zones and managed by a single fan with manifold.
- Secondary air injected through lateral nozzles above the grate to optimize combustion.

Fixed Grate Combustion System
Traditional fixed grate combustion system with bottom feeding
- Refractory steel grate elements, for long grate life at high operating temperatures
- Screw with Optimized Flights, so as to ensure constant and well-distributed feeding across the entire grate to maximize combustion efficiency.
- Dedicated burner sizing, according to the following critical parameters:
- Required nominal thermal power
- Fuel type
The fixed grate technology allows the combustion of dry materials and reduced particle sizes, ensuring high efficiency and ease of use

Plant Management
The management of the entire plant is entrusted to a PLC software developed over the years and optimizable for each installation.
The software allows complete control of the plant even remotely, in particular:
- Manages the smoke extractor via inverter to ensure constant negative pressure in the combustion chamber
- Manages all combustion air fans via inverters to optimize combustion in every phase
- Manages the fuel supply via inverter, modulating the quantity introduced into the boiler to achieve a wide range of available power based on thermal consumption
- Detects all main parameters through sensors for full plant control, specifically detecting:
- All temperatures of Water, Smoke, Combustion Chamber
- Feed system temperature as fire safety
- Lambda sensor for oxygen management in the flue gases
- Combustion chamber negative pressure
- Fuel presence sensors
Cleaning and Maintenance
The MR generators are designed for easy maintenance management, thanks to:
- Wide access doors for easy inspection of the heat exchanger.
- Ash extraction system optional, from the combustion chamber to reduce manual interventions.
- Pneumatic tube bundle cleaner: Reduces the frequency of routine cleaning interventions
Power Range and Configurations
- Available power: from 300 kW up to 6 MW.
- Construction type:
- Monoblock up to 2MW
- Two sections for higher powers

Optimal Industrial Applications
The MR series generators find optimal application in industrial and commercial contexts characterized by:
- Medium-high thermal requirements with relatively constant load profiles
- Availability of biomass with homogeneous characteristics
- Need for systems with high reliability and operational autonomy
- Need for energy cost containment and carbon footprint reduction
Main application sectors:
- Wood and furniture industry
- Industrial processes requiring hot water
- Small and medium-sized district heating networks
- Greenhouses and agro-industrial applications
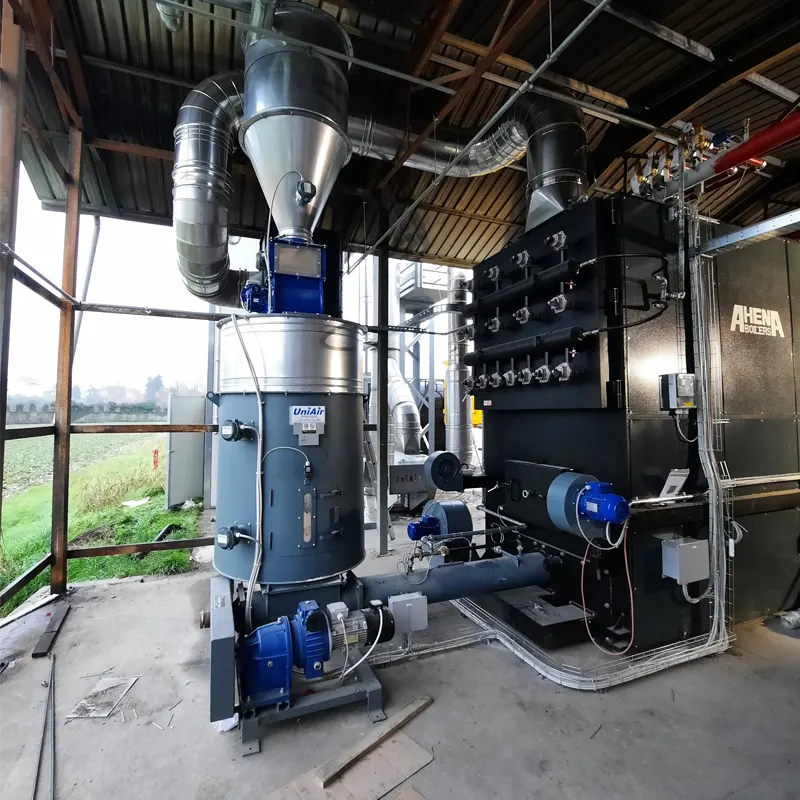

